Valve packing is a necessity for plants trying to contain product and meet the latest emission requirements. However, finding a sealing product that works and has longevity can be a challenge.
Graphite-based packing can be a good choice for stem sealing when elevated temperature requirements are necessary. This is due to graphite’s ability to maintain its sealing properties at temperatures that cause polytetrafluoroethylene (PTFE) to break down and allow leaks to occur. However, graphite is not an electrical insulator like PTFE; graphite will act as a metal and undergo galvanic corrosion if the environment is right.
Maintenance can be a hassle, magnified by the discovery of a corroded valve stem.
When a valve stem undergoes galvanic corrosion, the packing is no longer effective and leaks can occur. It also becomes very difficult to continue using the corroded stem when the valve needs to be repacked. However, if the stem is corroding, it is because the conditions are such that it is easier for the system to rust than stay as the perfect stem originally installed.
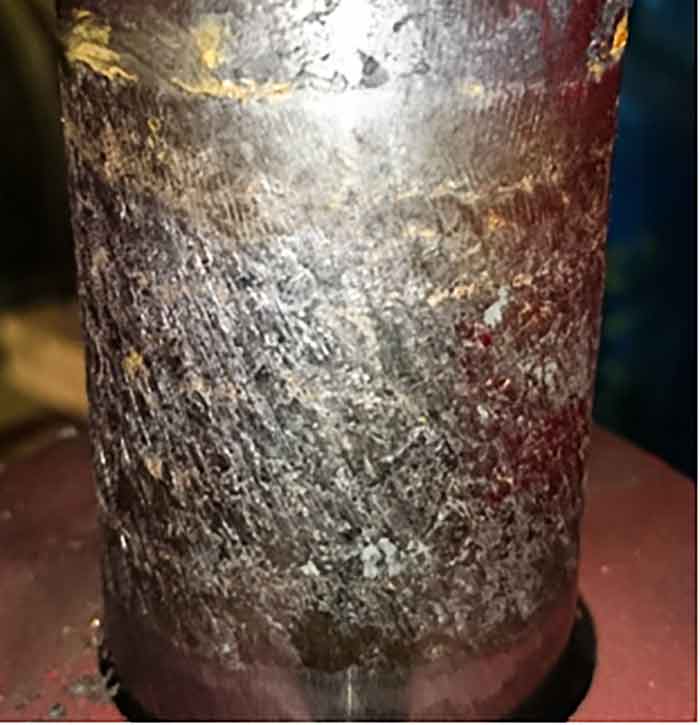
Image 1. Corroded stem. (Images courtesy of FSA)
Noble v. Less Noble Metals
When different metals are in contact with each other, in the presence of an electrolyte, galvanic corrosion can occur. The electrolyte acts as a hydrogen source in this system, helping one of the metals (the less noble one) to corrode. The other more noble metal will not corrode. If a metal is “more noble,” it will be happier staying itself. If a metal is “less noble,” it will be happier giving up its electrons and corroding. When looking at the galvanic series, the list of metals has one end that is “active” and the other that is “passive.” This is the same idea as nobility. Metals that are at the active end are happier oxidizing than the metals on the passive end. The farther away from each other on the series the metals are, the more likely they are to corrode.
Graphite packing is common for sealing valves with stainless steel stems. Since graphite falls on the passive end of the galvanic series, this match can cause corrosion of the stem if an electrolyte is present within the stuffing box.
In this case, the stainless steel (especially 410) is happy to give up its electrons to the graphite. This causes corrosion of the stainless steel, damaging the valve stem. The electrons move to the surface of the graphite and react with hydrogen ions present in the electrolyte. Therefore, the more acidic (more H+ ions), the worse the corrosion will be.
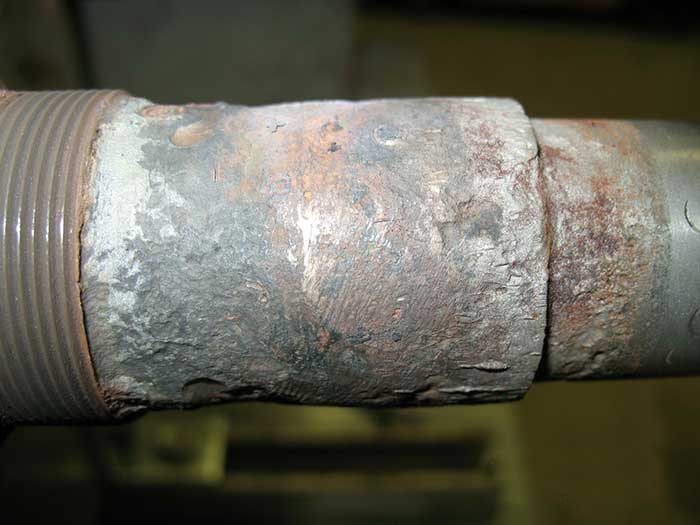
Image 2. Corroded pump shaft.
Preventing Corrosion
There are a few tips for preventing corrosion in valve stems. First, make sure the packing has a corrosion inhibitor present. A corrosion inhibitor is essentially a substance that enters a system where corrosion would have taken place and changes it in a way to make corrosion undesirable. How does it do this? There are several tactics to alter a system and prevent corrosion.
There are corrosion inhibitors that act as sacrificial anodes. These are less noble metals than the metals normally present in a system. Zinc is commonly used because it gives away electrons before stainless steel will. Think of it as sacrificing itself to protect the stainless steel until it has completely corroded.
The problem with this type of protection is that, once the sacrificial anode is gone, the stainless steel is no longer protected and will start corroding. Therefore, there is a specific amount of time where corrosion inhibitors are helpful, then they become useless.
Other types of inhibitors have more longevity than sacrificial anodes by providing an interruption on either the anodic or cathodic sites, preventing the transfer of electrons. These are like a roadblock for the electrons. The inhibitors create a thin film or passivation layer to keep the system from undergoing corrosion. These inhibitors are ideal for packing because they do not run out like the addition of zinc or another sacrificial metal would. This helps prevent corrosion over the lifetime of the packing installed.
Best Practices
Regardless of the presence of a corrosion inhibitor, there are best practices to be aware of to help prevent corrosion.
When the stuffing box and packing are wet and then placed in storage, corrosion can occur. While there is a corrosion portion of API 622, it calls for demineralized water. Therefore, if the water in the stuffing box contains any additives or contaminates, the resistance to corrosion will not be the same as documented in the API 622 results. If there are contaminants or a pH difference (especially if the water is acidic), corrosion will occur more rapidly than experienced during the API 622 test. By eliminating the presence of water, the corroding environment is also eliminated, and the stem will remain new and ready for use.
Sometimes a stem material change is necessary. In the case of 410 stainless steel stems, switching to 316 stainless could be enough to fix the corrosion problem. Other stem options that are closer on the galvanic series to carbon can be another option.
While galvanic corrosion can be a huge headache, there are prevention methods. Maybe new storage techniques need implementation. Maybe finding a new packing material that contains a corrosion inhibitor will solve the problem. Galvanic corrosion can be an issue of the past.
References
1. Demopoulos, G. (2015). Course Notes Corrosion and Degradation of Materials. Montreal: McGill University.
2. Substech.com. (2019). Corrosion inhibitors
3. Substech.com. (2019). Galvanic corrosion